Week 1/20-1/24
- tazam257
- Jan 23
- 5 min read

This week was a very turbulent week in terms of progress on the shopping cart. Starting off with Tuesday, because we had Monday off due to MLK day, I began by reprinting and changing the measurements on the coupler again. The coupler has gone through several iterations at this point so it made it all the more fulfilling once I had gotten it perfectly done. I'd done 6 different prints taking around 2 weeks to get through all those prints due to the extended process of resin printing. There were three main areas of issue with the couple design which was the hole where the coupler goes on the motor shaft, the hole where the couple goes on a protruded part of the micrometer, and then there are two holes on the sides of the coupler for bolts to go through which allow for the tightness of the coupler to be adjusted. Usually the problems with the coupler would be that it would not fit on the micrometer or the motor hole would be too loose or even the the space for the nut would be too large but I finally perfected the sizing on the entire coupler. However the stage has two different micrometers meaning two couplers are

required. I still have yet to print the other coupler because I ran into some issues with the resin printer while printing today. It had an error where the mixing bar got detached and was never resolved so I didn't get to actually print the coupler. Other than the the coupler I was also working with my steel finally. Last week I managed to get three out of four of the holes drilled into my steel. The holes are not perfectly centered on the steel bars which at first looks like a mistake but it had to be like that because the holes I had originally drilled in the shopping cart frame were not perfectly in line with each other. Drilling each of the holes on the drill press took a little bit of time with each hole because it is eighth inch steel which generates a lot of heat so I had to peck and take my time with the holes I drilled. Before I got to drilling the hole however I spent some time on fusion relearning a couple very useful tools it offers. There was a glaring issue with the design of the shopping cart engine and axle mount which is that fact that it is not very structurally sound. I'd learned how to use the stress simulation software in fusion and ran a couple tests and saw that the current design I had would see a whole lot of permanent deformation and potentially snapping so I had to come up with a solution. I spent a day reteaching myself how to use the sheet metal tab in fusion to make these bars which would connect to the square steel tubing and the frame of the shopping cart and act as compression bars stopping the tubes from bending upward. However after modeling all that I ran the simulation and saw that it literally did not change a thing and the entire idea was scrapped. I deleted the entire thing so I have no pictures of it. Next week I have to think up another idea for the frame to make sure it doesn't break under the force which I calculated to be 880 Newtons of force but that's also a very rough estimate and nowhere near exact.
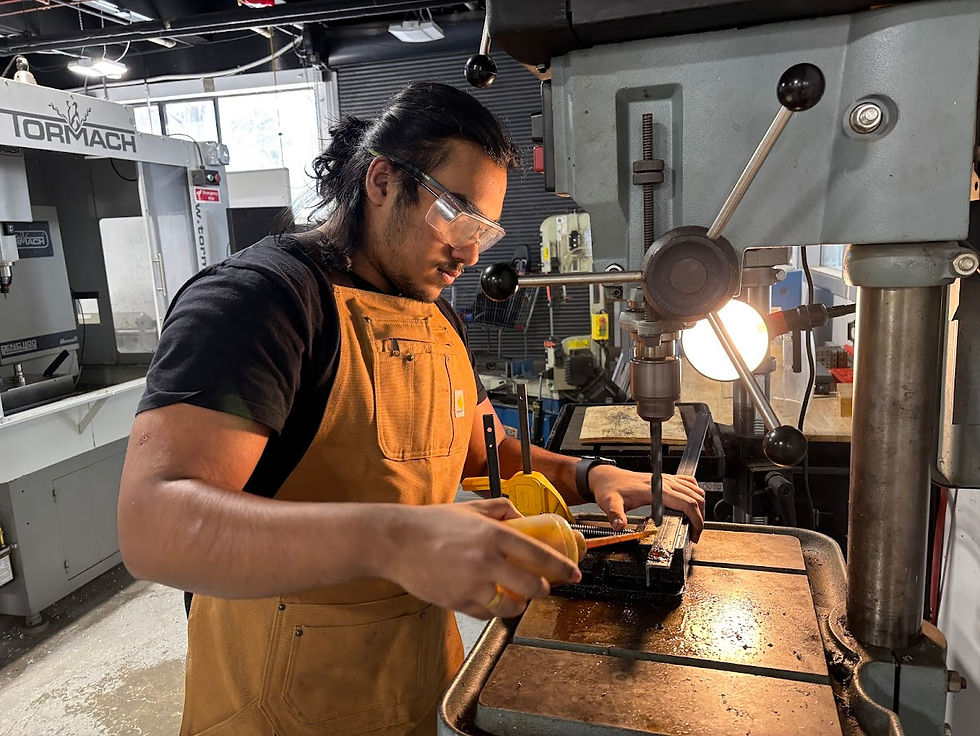
There was some issues I came across while drilling the holes though. Some of the holes when I was drilling them the drill bit would make some bad noises that did not sound great like very high pitched scraping. In the end the holes all came out fine they were a little rough but the file took care of that. So I had drilled the holes out to be a half inch on the steel and in the shopping cart frame but for whatever reason the holes drilled in the shopping cart frame were able to fit a half inch bolt but the steel couldn't so I had to search for a bolt that would be adequate size. Ultimately I settled on a three eighths inch bolt because it was the only bolt I could find enough of that were also long enough to pass through the frame of the shopping cart.

The bolts managed to make it through all the way which was a relief and it took a bit of rummaging to actually find bolts that were the perfect length. But then I went to measure the distance of the bars from edge to edge and I found something that was very disturbing. One side measured five inches apart but the other side measured five and a half inches. The holes were crooked. But I thought maybe it's just because the bolts are in holes larger than was meant for them so I undid the bolts on the longer side and tried holding the bars as close together while bolting them in and I saw no change. I flipped the bars over and tried again, no change. I then took a caliper to the holes on each side and saw that from inner edge to edge the holes were almost four tenths of an inch apart from each other.

But before I got to fixing that I decided to help out Ben Wirz with something he was taking on which was reorganizing the drill bits drawers. What happened with him was that while drilling some holes into a part for the stage he found out that he had grabbed a drill bit that was not supposed to be in the bin he took it from but it was too late at that point so he had to roll with it. So I spent about half an hour helping him reorganize and sure enough many drill bits were just not in the right place. Understandably the smaller the drill bits got the more unorganized they'd become but still it was many drill bits that had required reshuffling. After reorganizing I took to the task of actually fixing the holes I had drilled.
The solution I settled on was filing the hole

until the bars were equal length from each other on both sides. So I had to file away around a quarter inch to half inch of the hole away to get the bolt to be in the right spot. Honestly there isn't that much I can talk about with this. I sat on the floor of the machine shop with a file for over an hour filing and filing and filing. By the end of the day I'd gotten the distance from five and a half inches to around five and a little less than a quarter inches.
Commentaires